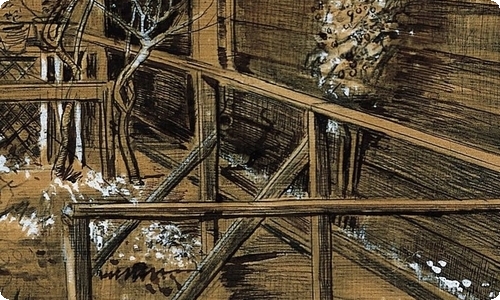
4月20日大修,质检车间吸取了历届大修经验和教训,面对这次检修时间紧、交叉作业多、战线长的检修状况,为了更好的配合各车间装置的检修工作,车间对全厂重点,关键部位进行分析,讨论。组织全车间人员对大修期间的工作重点及注意事项进行学习。通过PPT讲解,动火及受限分析注意事项,让没参与过检修的新员工对大修安全分析工作有基本的认识。同时,车间利用下班时间组织白班人员在造气,净化等装置区进行实际操作,为完成大修任务做了前期准备工作,此次大修质检车间以较高的质量完成了检修安全分析,以及大量常规分析工作。现将这次检修安全分析和开车准备工作汇报如下:
1、现场检修安全分析
在检修期间安全分析点多面广,特别是造气、甲烷分离和合成、净化四个岗位是这次检修的重点。质检车间按检修情况,分别在造气、甲烷分离和合成、净化设置四个分析点,人员24小时值班,现场交接,同时从常白班抽调精干人员5名、运行班组各抽出3人,配合当班期间检修安全分析,确保安全分析随叫随到。经过大家的共同努力,圆满完成了安全分析工作,并为以后检修期间如何做好安全分析积累了经验。
检修期间对所有色谱进行了重新标定校准,确保仪器分析准确及开车后仪器正常运行;对水分析岗位上的PH计、电导率仪、浊度仪、硅酸根、磷酸根等仪器进行维护及标定,以确保开车分析数据的准确性。
通过梳理车间大修及开车工作,发现一些不足之处,主要有以下几点:
1、由于车间新员工较多,对现场装置熟悉度不够,与各岗位主动沟通不够。
原因:检修前期,质检车间虽然认识到分析取样点多,并加派了分析人员,但由于车间新员工较多,对现场装置熟悉度不够,与相关车间沟通不够,导致个别作业点因此而滞后。
改进措施:加强对各工艺现场的培训,结合各岗位分析项目及特点,及时与相关车间沟通,全面考虑问题,合理安排工作,确保工作有序开展。
2、安全分析仪器损坏严重,大修期间安全分析工作量大、工艺介质复杂,管道容器内存在蒸汽,导致四合一仪器吸收泵故障、传感器失效。
改进措施:加强员工对分析仪器操作培训,现场安全分析时,询问工艺人员管道容器是什么介质,采取积极主动措施保护安全分析仪器。
3、新员工安全意识淡薄,对安全认识不足。
新员工对装置区的危险因素不清楚,可能会发生自身安全事故。个别新员工在做受限分析时,身体置于受限空间里面进行测定,存在很大的安全隐患,按照规定未分析合格的受限空间不能进人。特别是针对新员工及对装置不熟悉的员工进行重点培训,让他们懂得正确的操作,明确危险因素发生的原因,使安全意识深入每位员工。
4、班组交接班不清楚,导致安全分析不及时。
在停车检修期间,有许多分析是连续进行的,有时班组在交接的过程中没有交代清楚,致使受限空间分析未按时分析,进一步完善交接班制度。